Habitat for Humanity, renowned for transforming homeownership dreams into reality, has taken a groundbreaking step towards enhancing affordability through 3D-printing technology. Since its establishment in 1976, the organization has erected numerous affordable homes for those in need. The latest achievement involves the completion of their inaugural 3D-printed house in Williamsburg, Virginia, using automated computer technology and a proprietary concrete mix. April Stringfield and her 13-year-old son, the proud owners of this innovative dwelling, eagerly anticipate turning it into a warm and welcoming home.
While 3D-printed homes remain a rarity, the success of the Williamsburg project underscores the growing interest in constructing cost-effective homes while preserving natural resources, particularly trees.
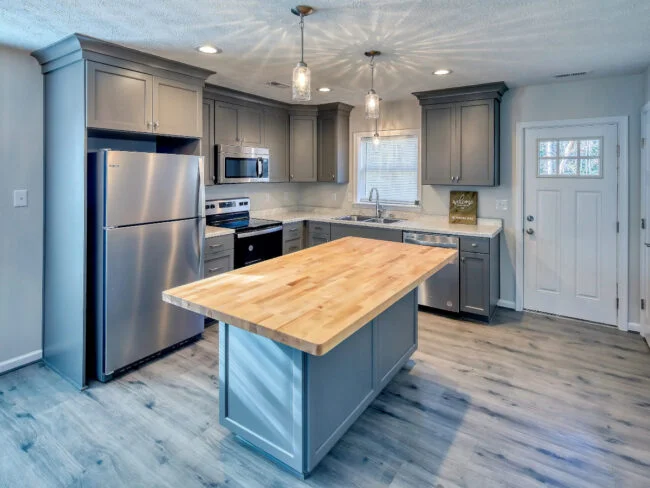
A Conventional Abode
Despite the unconventional method of printing walls instead of stick-framing, the Williamsburg house stands as a typical residence. Spanning 1,200 square feet, it encompasses three bedrooms, two full bathrooms, and a covered front porch, providing a delightful space for Stringfield to savor warm summer evenings. The incorporation of traditional siding on the roof gables and standard bricks on the porch pillars maintains the familiarity of a regular home. As an added bonus, Stringfield received a 3D printer enabling her to craft custom cabinet hardware and light switch covers.
Cost-Efficiency through 3D Printing
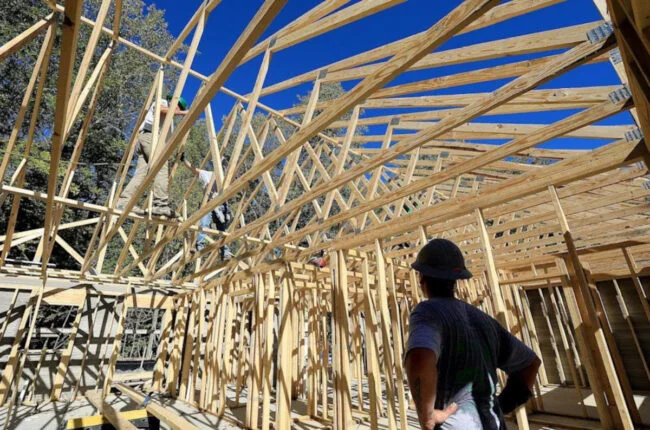
Amidst the pandemic, soaring building material prices, exacerbated by supply chain disruptions, led to a doubling or tripling of costs, significantly impacting homebuilding expenses. By opting for concrete over wood, Alquist, the contractor responsible for printing the walls, managed to save an estimated 15 percent per square foot for Habitat. While labor costs for constructing a Habitat home are covered, homebuyers contribute towards the expense of construction materials. The cost savings achieved through the use of concrete are consequently passed on to the buyers.
The Printing Process and Personalization
Impressively, the concrete walls of Stringfield’s home were printed in a mere 28 hours using Alquist’s patented concrete mix and advanced extrusion machine. The walls, fortified with steel during printing, undergo sealing with a clear or tinted coating, preventing moisture transfer through the concrete. Homeowners can opt for the standard gray concrete or choose from an array of earth tone hues, providing a customized appearance.
Traditional construction steps follow the printing phase, encompassing roof installation, plumbing, wiring, and interior finishes. In adherence to Habitat’s guidelines, Stringfield contributed 300 hours of sweat equity, underscoring the collaborative effort involved in making her new home a reality.
The Habitat Buyer Program
While the Williamsburg dwelling marks Habitat’s debut in 3D-printed homes, it is likely a precursor to future endeavors. The Habitat buyer program plays a pivotal role in facilitating homeownership for those unable to pursue conventional paths. Prospective homeowners commit to contributing their time to the project or at a Habitat ReStore, gaining valuable insights into budgeting for mortgage payments and home maintenance. The nonprofit, with a nationwide reach, ensures fairness in the selection of homebuyers.
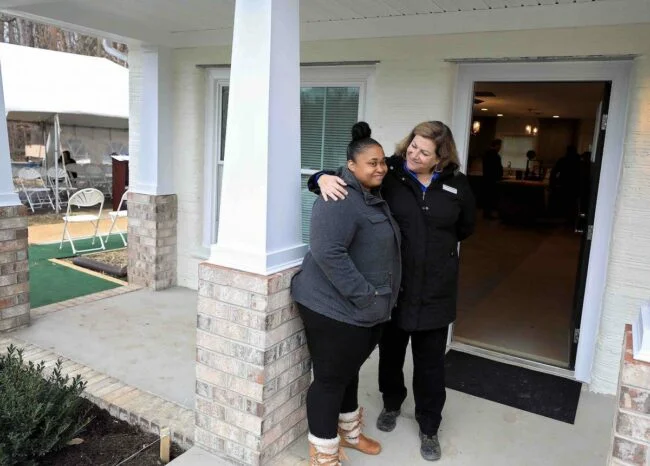
Paving the Way for 3D Construction
The realm of automated 3D printing for homes is in its early stages, but the landscape is evolving. Computer-constructed homes, like the one in Riverhead, New York, are already available to the public. Nevertheless, standard construction methods persist in most communities and are likely to dominate in the foreseeable future.
Stringfield expresses her elation over her new home, emphasizing her gratitude for the backyard where her son can play and her puppy can roam freely. As Habitat for Humanity pioneers 3D-printed homes, the Williamsburg project sets the stage for a future where innovation and affordability converge to provide sustainable housing solutions.
image source : habitat pgw